Jump to:
Real-Time Data Tracking During Welding Operations
What if someone told you it is possible to capture welding data for each weld joint on a particular structure? You can see everything from amperage and voltage information to data that show specifications have been met. Sounds too good to be true, right? It’s happening and helping manufacturers in the military, offshore and onshore wind, shipbuilding, nuclear, and more industries prove they’ve welded structures to original equipment manufacturer (OEM) specifications and streamline approval processes.
Adopting an automated approach to one’s welding operation is the first step in the process. Without automated welding processes, especially software into which all preliminary data is entered, real-time weldment data capture is impossible.
Specifications Direct Weld Paths
Pemamek Oy’s WeldControl 300 software has been capturing data for 27 years. The software is available in three modules: OLP for offline programming, CREATE for entering measurements and features parametrically, and SCAN for creating 3D models using data captured via laser scan.
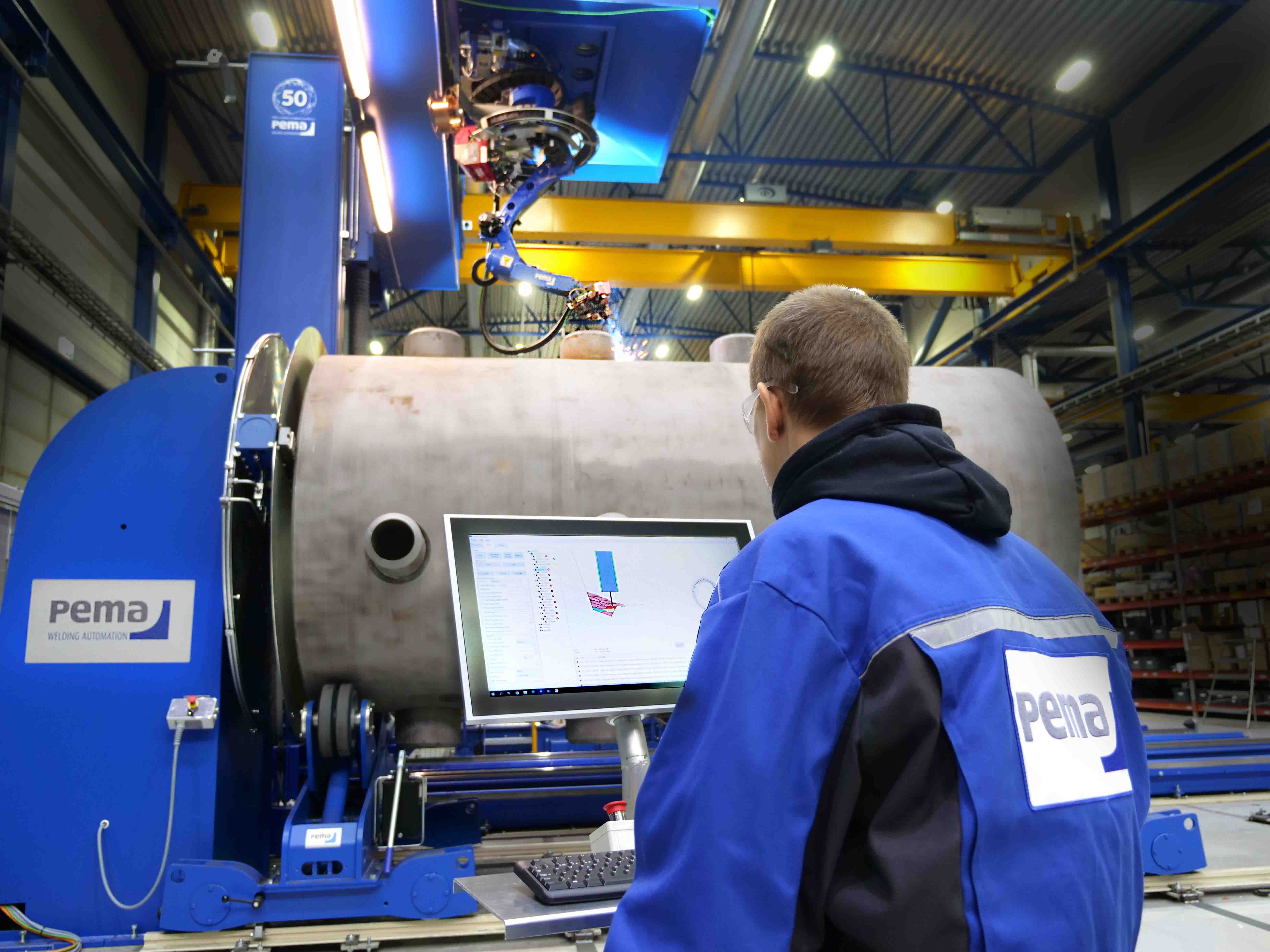
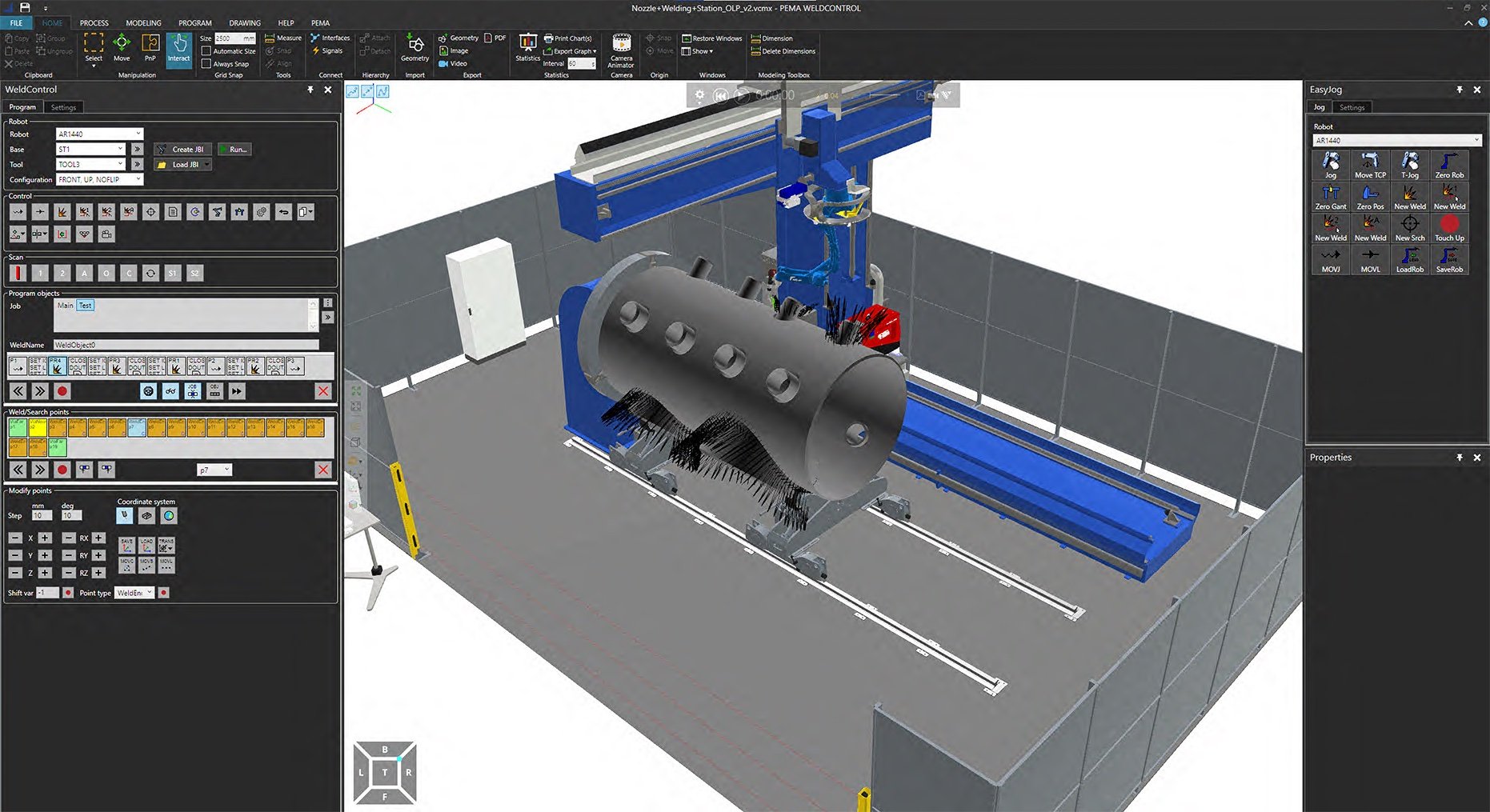
When specifications set forth by the customer are entered into the software’s system, weld paths are created automatically, directing robotic welding arms to complete the process. While this is happening, operators know exactly where the workpiece is at any given time and place and capture data as it pertains to amperage inputs, voltage, and movements.
“It’s critical to understand that the welding power source sees differential in the amount of amperage that is applied, and that amperage changes based upon the physical attributes of the workpiece,” said Michael Bell, Pemamek LLC North America sales director. “We capture that data and, as soon as we see a change or trend in amperage and any voltage changes, we’re able to adjust either movement or wire feed and/or heat input.”
Because data is captured at every centimeter of the weld bead, the point at which any anomalies might occur is pin-pointed. This is especially helpful with multipass welds. Bell suggests that users establish a standard heat range or amperage input or voltage range in their welding procedure specification or procedure qualification records.
Data Captures the Critical Parts of a Weld Joint
While data capture is possible for nearly all heavy-duty welding operations, it’s especially useful for critical weldments for offshore wind structures. Parameters are often set by the operator of a wind farm who engages a subcontractor to manufacture the components comprising large monopiles or platforms supporting large wind towers. For example, the structure needs to be able to sustain a 50-kJ Charpy test at –50°C, which, according to Bell, is a typical impact-resistance test. During welding, all data is captured and then exported in virtually any format.
“If there are 200 passes, for example, manufacturers can transmit the report via the cloud or paper to their customers so they have data following every weld joint, giving the customer peace of mind,” said Bell. “Even if ten years go by, we can still find the exact data and position of a weld and do a field repair, being able to zero in on where it is and how it was originally done.”
Options for Real-Time Detection Anomalies
Detecting anomalies can be done in real time. When problems occur, the software can throw an alarm, leaving the operator with several options to fix the issue. First, the entire weld can be stopped; however, Bell does not recommend that option. Second, a data capture can be set up to identify the particular piece of the weld so a repair can be performed before the next pass. Finally, a notation can be made that an anomaly exists and has the potential to be an issue down the road but can be repaired later.
“We have a book the customer can refer to that shows weld layers and the location of any anomalies,” said Bell. “It’s a huge database that can be used for future reference to assure quality to the manufacturer’s customer.”
Quality standards are also set forth by the OEM. Reports can be generated in any format as a written assurance that all standards have been met. At first glance, that might be commonplace. But with the data generated using the WeldControl 300 system, customers can determine at which point the Charpy test was performed, whether errors occurred at any point on each of the weld joints, and whether welds were performed within the specified parameters every step of the way.
The ability to capture raw data can play a significant role in reshoring manufacturing operations. “As we work to on-shore these weldments, it’s imperative that manufacturers are able to prove they can capture data and meet the criteria set forth by OEMs in the United States or Europe,” said Bell.
Conclusion
The ability to capture data at each stage of a weld, especially multipass weldments on very large structures, makes it easier to pinpoint anomalies, note successful operations, and create a big book of crucial information that can provide strong approaches to welding and show that all standards have been met and/or exceeded. This is only possible by investing in a fully automated welding system capable of handling large amounts of data and communicating it to the system. It is also important to work closely with the system supplier to customize the operation to the manufacturer’s needs, tweaking it as necessary.
This article was written by Marie Pompili (owner of Gorman Pompili Communictions LLC, Hudson, Ohio) for the American Welding Society.