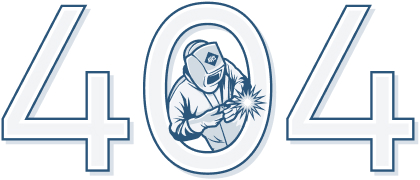
Oops! 404 Error
We can't find the page you're looking for
The page may have been moved, renamed, or temporarily unavailable
please check the url and try again.
If the problem persists, please contact AWS Customer Support.
Oops! 404 Error
The page may have been moved, renamed, or temporarily unavailable
please check the url and try again.
If the problem persists, please contact AWS Customer Support.